合理安排线切割工序,对于提高线切割加工生产效率具有重要意义。合理的工序不仅能减少加工过程中的人为干预,避免因策划不当或是对参数把握不准而带来的停机,而且还可以充分利用线切割机床自动设置加工参数的功能。
(1)先易后难,自我确认以多工位级进模具的模板加工为例,先从容易的、对误操作敏感度低的地方开始。比如先加工固定板,再加工凹模板,最后加工卸料板,这样操作者比较容易建立起信心。因为,对于用卸料板导向的级进模来说,它的重要性与模具.上其他零件的关联度最大。如果一开始就加工卸料板,对设定的偏移量与实际值之间的偏差把握不准,或者对机床的状态不清楚,一旦切出的型腔与凸模配合的间隙过大,这块模板就会彻底报废。相比之下对固定板要求的间隙就宽容得多,即便加工中有些失误也能挽回。
在同一块模板的加工过程中,也可以本着这种先易后难的原则。从简单的、容易在机测量的、公差带较宽的中小孔开始切割;在确认了设定的参数是正确的之后,便可以从容地完成后面所有型腔的加工。
(2)充分利用自动穿丝功能使用带有自动穿丝功能的线切割机进行多型腔模板加工时,要根据型腔的大小来决定断口的留量,在无人看管的情况下不切断废料,加工到暂停点,自动剪丝后,走到下一个型腔继续加工,直至完成所有的型腔。然后,在有人监视的情况下,重新启动或调用程序,逐个切断并-- - 取出各自的废料。当全部废料取出之后,机床又能够自动进行后续所有型腔的再次或多次切割,恢复到无人监视状态。
断口的留量取决于型腔的大小和切断时的轨迹方向。废料自重产生的弯矩越大,断口应留得越长。有时,一个型腔可以分为几段,由不同的穿丝孔来引导,目的为了减少弯矩的不利影响,如图1所示。
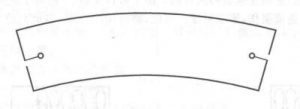
图1对大型腔进行分段加工
如果设计了专门的切断程序,穿好丝之后,就可以用最短路径,沿相反方向将废料切断,这时的断口保留1 mm长度或更短- -些即可。如果顺着原有程序路径重新回到暂停点,就必须保证要切掉的废料与型腔之间必要的连接刚度,才能使切缝的宽度不会因材料变形而发生太大的变化,电极丝就可以不带电或仅以弱规准加工至暂停点,等候切断指令。
(3)根据工艺特点,选择不同的加工排列成批 加工凸模或零件时,两种走丝形式的线切割机由于它们对冲液方式的依赖程度的不同,使得对加工顺序的排列有所不同。
高速走丝线切割加工时,由于不需过多地考虑冲液方式是否得当,加工顺序的排列显得不是十分紧要,如图2(a)所示散热器翅片电极的加工。先把一个方向做好,取出废料,再通过转动夹具90°,完成另一个方向上的切割。
低速走丝线切割加工如果也像图2(a)那样来加工就会有问题。在第一个方向上,切割会因上下喷水嘴与柱面之间封不住水,而丧失了压力冲液的条件,加工速度会成倍地降低,尤其是对非浸液式的加工;在转动了90°后的第二个方向上,同样不能实施高压冲液,因为压力过高会使靠近上下水嘴的电极片弯曲。
图2(b)是为适应低速走丝线切割对冲液条件的苛求而采取的加工顺序。在工件毛坯上先用其他工艺手段加工出一-对平行表面,厚度比最终尺寸增加一个变形修正量和若干次修切的加工余量,在调转90°之后,这对平行表面无需用大电流再次粗切,也没有排屑问题。另外,为防止喷水嘴与工件发生碰撞,电极根部在铣削加工时要向后多移出一段距离。这样,工件装夹好后喷水嘴就能贴近工件表面,用上下冲液方式,先加工出带有弧形的轮廓,再加工出梳型轮廓,使得第一次切割时就能用上较高的冲液压力、又不至于使高压冲液对第二次切割造成影响。
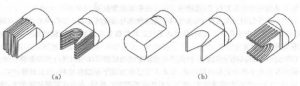
图2两类线切割机床采用的不同加工顺序
又如,批量加工消耗性的电机冲头。用高速走丝线切割可以加工一批,切断一批,最后用磨削的办法统一进行断口处理(图3(a))。用带有自动穿丝的低速走丝线切割机床加工,务必不要使一组冲头的数量太多。因为,如果加工中排列的冲头数量太多,一旦中途出现断丝,就得回到起始点,重新穿丝后再次切割。由于材料变形、冲液的干扰作用,多次放电会对已加工好的冲头表面造成损伤,影响精度。所以,最好用小分组、多单元的方式来进行加工排列(图3(b))
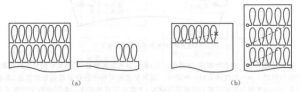
图3两种不同冲头的加工排列
(4)规模生产时,编程与加工作业分离一 人多机生产时,编程和加工作业必须加以分离,这样可以提高各自的专业技能,减少出错的概率。模具零件专业化生产时,编程与机床操作混合作业如同驾车时打手机,肯定会增加运行的风险。
(5)提高机床无人化生产时的加工成功率无人化生产时,尽可能选择轮廓简单、切割面积大、形状单一.具有-定批量的工件进行。对于复杂的级进模具的模板加工而言,如果上面的型孔小而多,每个轮廓的加工时间不长,最好是在有人监视的情况下完成第一遍的切割,取出所有的废料之后,再恢复到无人操作状态。
尽管也可以在每个轮廓上留下暂停点,最后在有人的情况下一-并切断。但是,这样等于多增加了一次穿丝、上下水、启动、停止所需要的辅助时间,总的算下来未必省时。尤其是当工件上穿丝孔的位置有偏差,不能保证自动穿丝100%的成功率,无人化加工过程被中断的事是经常发生的,从而导致了计划完成的时间后延,影响模具的交货期。
(6)减少线切割的过度加工既然电火花线切割加工的速度慢,那么零件加工能用其他工艺完成的就尽量不要用电火花线切割加工,能用一次切割完成的就不要用多次切割。
以凹模镶块为例,其外形既有精确的配合尺寸,又有很高的几何精度,用精密磨削加工要比用电火花线切割机直接加工效率高得多。要保证型腔与外形有很高的位置精度,除了用一次装夹和同时加工出内外形外,还有很多其他的工艺方法也能实现,效率更高。
电火花线切割加工断口应尽可能留在平面上,便于用磨削方式来快速处理断口。
进行凹模型腔加工时,先切割出落料斜度,再用多次切割精修刃口,尽量减小精加工面积。
对于同一轮廓线上不需要多次切割的线段,宁可编程时麻烦些,改变一下修切时的轨迹,也不要对没用的线段作无谓的精加工。
(7)压缩辅助时间花 费在线切割辅助时间上的主要作业有:装夹找正、程序读取.参数确认、废料取出、穿丝剪丝、液面升降、异常情况处理等。其中装夹找正所用的时间最长,尤其是对新手而言。为减少装夹找正的时间,选择适用的夹具、在机外做好预先的调定工作,能大大提高线切割工序的生产效率。
(8)加强对加工时间的预测与控制根据切割轨迹的长度,在编程时就可以估算出总的加工时间。
对于高速走丝线切割机床而言,知道了总的时间不仅能预计在多长的时间内完成,还可以估算电极丝的损耗对尺寸精度所产生的影响。
对于低速走丝线切割机床来说,了解总的加工时间可以根据以下几个方面进行:
①是否有足够的储丝量。
②各个加工任务之间在时间上的衔接。
③针对每项任务的工时分配合理性。
④在当前运行周期内对机床安排例行维护与必要的保养。
从而有利于对机床的工作状态监视、运行成本核算和模具工期控制等。
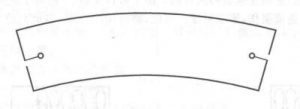
图1对大型腔进行分段加工
总之,任何影响加工周期的因素,都要认真分析,予以控制。如果在加工策划阶段就能系统地、并行地考虑上述有关问题,必然可以提高线切割加工的工作效率。