由于电极丝的直径和放电间隙的存在,加工时电极丝的运动轨迹都必须偏离工件轮廓一定距离,才能保证加工结果符合设计要求。另外,模具加工需要在不同的模板上根据相同的轮廓加工出不同间隙的型腔,可以按理论轨迹编程、通过直接修改偏移量来满足这一要求。
对于高速走丝线切割加工来说,偏移量(编程时的补偿量)通常为电极丝的半径再加上0.01 mm的放电间隙,习惯上比较固定。放电间隙虽受加工规准、工作液状态以及工件材料等物理因素影响,但在编程时一般都不考虑,常设定为一-个固定值。偏移量的更改主要是为了弥补较长时间加工后,正常损耗所导致丝径的减小。
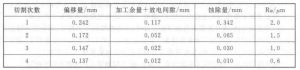
表1低速走丝电火花线切割机进行四次切割时的偏移量
对于低速走丝(含中走丝)线切割加工来说,加工规准、冲液状态、工件材料、多次切割时的预留量,以至放电时的热影响都会对偏移量的设置起作用。标准加工状态下的偏移量,在机床的使用手册中一般都有明确的数值,可以直接查询。表1是低速走丝电火花线切割机进行四次切割的偏移量,所用的黄铜丝直径为0. 25 mm,工件材料为厚度50mm的Cr12。
需要指出的是,机床操作手册上的设定值只是一种参考值,并不能满足所有的加工需求、替代人们在工艺上的不断探索与创新。因为,有许多变动因素导致了实际加工结果与标准状态不符:新旧机床在脉冲电源输出回路上不同的传输损耗;不同的工件材料及内应力分布引起的伺服状态改变;工作液电导率与冲液压力偏离校正状态;差异很大的几何形状;不同的电极丝质量、电极丝移动过程因摩擦阻力变化而导致张力的改变等。
在多次切割中,最后一次修切决定了零件的表面粗糙度,而第二次切割则基本、上决定了零件加工的尺寸大小,次后的修切对尺寸大小也有一些影响,但加工量甚微,这是设定多次切割中各挡加工余量的主要依据,也是平衡速度与质量要求的法码。
随着多次切割次数的增加、放电能量的逐级降低,在工件尺寸接近最终要求的同时,表面粗糙度也会明显地改善许多;如果表面质量变好了,尺寸精度反而变差的话,就要考虑加工余量留得是否合适。尤其是当工件厚度比较大时,精加工余量选择不当、前一次切割加工留下的形状误差偏大或是不均匀、甚至只有几个微米的差异,都会导致最终的尺寸精度恶化。规准越弱对加工余量的大小、分布的均匀程度越敏感。
所以,对重要的高大零件进行加工之前一定要确认各次切割中选用的偏移量是否合适,不单单是遵循使用说明书,一定要有经过验证的数据。否则,在实际的加工中很可能出现意想不到的问题,例如在工件表面上留下无法去除的深沟条纹或者母线的直线度不好,影响到最终的加工质量。